The key role of analysis and simulation in engineering processes: A new paradigm and evolving practices
Growth, Optimization, and Digitalization. These three priorities, identified by the manufacturing industry as central for the coming period, are closely interconnected. Growth and optimization are natural goals for companies aiming to stay competitive and respond swiftly to evolving market demands. Digital transformation is key to achieving success in both areas. With advanced solutions from Siemens Digital Industries Software, the defense sector can modernize its operations, tackling engineering and design challenges through robust design and development support tools.
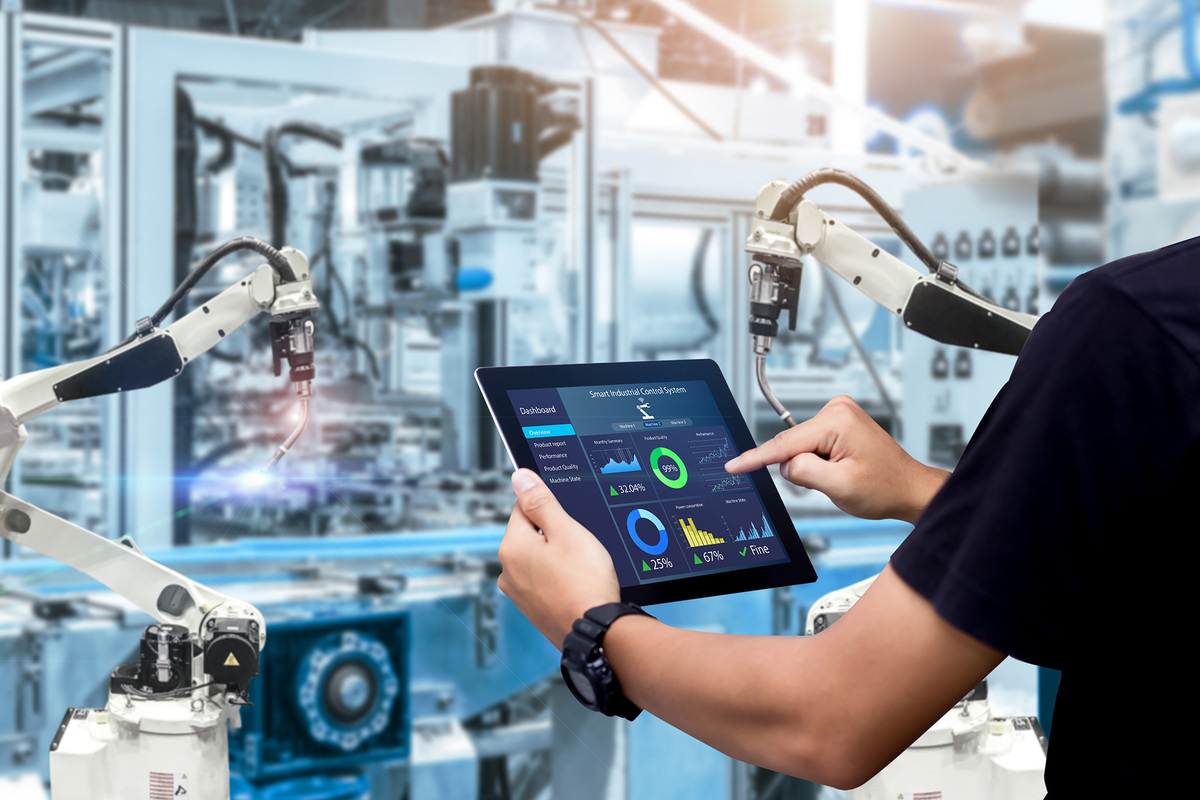
For years, industrial companies have invested in efficient resource management, cautiously incorporating digital and analytical technologies into product design. According to McKinsey, only 35% of aerospace and defense companies currently use these solutions to enhance the quality and efficiency of their engineering processes. But is this caution justified?
Simulation: The new battlefield
In the defense sector, solution development is tightly bound to specific functional requirements. Tactical and technical guidelines define the design framework, while customers increasingly demand faster design cycles. Designers dedicate significant time and resources to ensure that each project, whether for a combat vehicle or a soldier's equipment, meets stringent requirements.
A global trend reveals a growing adoption of digital analytics and simulation across industrial organizations, characterized by a gradual shift from physical prototypes to digital alternatives. By gathering essential data early in the design process, organizations can reduce time-to-market and minimize costs and risks, particularly those related to tactical and technical requirements. This approach fosters greater innovation, flexibility, and productivity, enhancing the availability of advanced products. A design process that integrates simulation and analysis with digital solutions supports error-free production from the outset, minimizing common early-stage product development issues.
Despite these advantages, the field of simulation and testing is still underdeveloped in the Czech Republic. This is largely due to the low awareness of local companies about the possibilities of digital tools. The belief persists that the necessary information can only be obtained during time-consuming physical testing of prototypes, which until recently was an indispensable step in engineering processes.
Experts at Siemens Digital Industries Software believe that changing the approach to the engineering process not only translates into greater efficiency, but also significantly increases an organization's return on investment.
A modern approach to product testing
In the world of new technologies, product testing using traditional models is no longer effective. Outdated schemes for checking product compliance with required standards neglect a number of contexts that are crucial for further decision-making and quality product development. The use of traditional systems leads to the discovery of errors only at late stages of production, when the cost of correction is much higher.
For areas such as defence, where complexity is a given, systems engineering is indispensable. Using a model-based approach facilitates accurate process control and continuous monitoring of decisions at every stage of product development. Based on a systems methodology in accordance with ISO standards, model-based systems engineering consolidates product architecture, interfaces, requirements and parameters in one place. Integrating models with other Siemens digitalization solutions ensures comprehensive product lifecycle management.
Process change, paradigm reversal
What the traditional engineering process looks like is largely determined by the capabilities and limits of the organization. It usually starts with what is called an initial model: an initial structure built on previous engineering experience. Experts develop a model which is then checked for various parameters according to tactical and technical requirements, i.e. strength, acoustics, thermal load, electromagnetic properties, energy consumption, available power capacity, etc. At this stage, companies usually face a major obstacle, which is the limited availability of people from the analysis and simulation departments.
This results in longer processing time for simulation-analytical tasks, delivery time and interpretation of results. Thus, it is common for engineers to receive analytical conclusions for the first revision of a project when they are already in the third iteration of that project, which they have been developing all along based on their own experience from previous projects.
This design and development process is repeated in ongoing development work. The processing time for simulations and analyses is not keeping pace with the pace of development. As a result, teams have to market an incomplete or untuned product that has only undergone partial validation. Up to 30% of the solutions implemented may not be verified due to delays. The fatal consequences of such an approach for the field of complex defence products are not hard to imagine.
Software specialists at Siemens Digital Industries propose a paradigm shift and the use of digital tools for analysis and simulation in the early stages of the development process. In a situation where we do not yet have a baseline 3D model, we can implement a process of complex system simulations. This should change the way engineers work, as they will be able to use simple functional diagrams to determine whether a given model will meet initial tactical requirements.
Access to this data offers engineers a significant initial advantage, allowing them to bypass costly product development paths by using digital analysis to assess the feasibility and resource implications of seemingly promising ideas upfront.
It optimizes redesign processes, where each version goes through analysis and simulation, avoiding the delays typical of the traditional design and development process model. It streamlines the development of a given model and sets limits on engineering work. Avoids the risk of errors by early validation of unusual and testable solutions that could negatively impact the product at any other stage of the development process.
As a result, the project implementation time is reduced. When we have concrete simulation results, we can assess the quality of the project and eliminate unexpected errors related to the use of the product that may be unnoticeable in the first stages of the work. All of this translates into a noticeable acceleration of the organization's engineering processes and an increase in product quality and innovation.
The importance of the right tools
Changing practices in the design and development process also bring specific requirements. Only the right tools that ensure perfect data exchange can truly increase efficiency by eliminating the unnecessary repetition of development errors. Attention must also be paid to the availability of analytical and simulation resources. The limited number of simulation specialists is one of the main obstacles to optimising the development process today. Improvement in this area requires the implementation of tools in a unified environment, with a low barrier to entry and also easy to train.
Tools that meet such criteria while allowing access to a sufficiently large amount of information can significantly reduce the development process time. It is possible to perform simulations based on an initial model, without full documentation or a 3D model. This translates into a noticeable acceleration of work and facilitates the development of projects in accordance with tactical and technical requirements.
The Czech defence sector has also seen a "shift to the left"
The process of marketing a product in the defence industry is influenced by many variables that organisations have to take into account. The resulting time and cost of change is higher the later the change takes place. As the project progresses, the scope for implementing structural changes decreases and the difficulty of correcting identified errors and problems increases. For this reason, a worldwide trend of 'shift-left' has emerged. Companies try to take as many measures as possible early in the engineering process, when the opportunities for change are greatest, adjustments are least complicated, and the project can be subjected to major re-engineering.
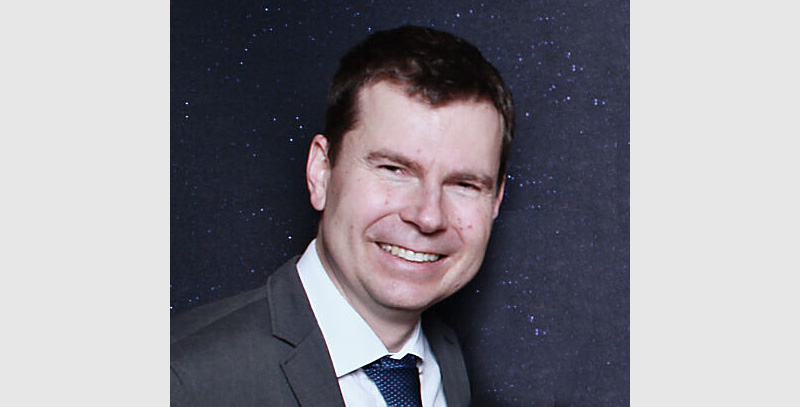
Investment in product design and engineering tools, including a suite of simulation and test analysis solutions, is critical in the highly competitive defence market. These tools can be seamlessly integrated into a variety of environments, enhancing their overall capabilities. This is an excellent opportunity for the Czech defence sector, and one that is well worth exploiting.
Zdroj: defence-industry-space.ec.europa.eu, accenture.com